To successfully reduce costs in the implementation of a CO2 system, either with the intention of replacing an HFC system or for new installations, it’s essential to start the project from a global approach before starting with the technical part and the specific conditions of the project.
That’s why a correct package of basic engineering, detailed engineering, calculation memories and subsequent estimates and parameters according to preset ranges. By means of a correct basic engineering, the efficiency of a system can be estimated according to the refrigerant used before incurring greater expenses.
How important is the design of a cooling system?
A good design will obtain studies of electrical network, future extensions, physical location, and orientation of the electric station with respect to the lines, and other requirements such as single-line diagrams, equipment layout, dimensions, definition and specification of these equipment as well as its basic functional schemes. These documents give guidelines for the selection of later devices involved in the proper functioning of the system serving as interconnection between the various teams, these choices are key to achieve a true reduction in the cost of the work.
How is the cost of a CO2 cooling system optimized?
An efficient way to achieve savings in CO2-based cooling systems is through the commissioning process commonly known as "commissioning" with subsequent continuous monitoring. This process starts by testing the system pressure and once the gas has been charged and isolated, the initial start-up, calibration and optimization begins.
Before starting the commissioning process, all visual observations and adjustments must be recorded for future reference.
The system will begin to cool down as soon as CO2 in the liquid state is loaded into it. This causes the pipes to contract, with possible cracks between its joints. The entire system must be inspected for any signs of leaks.
Before starting the commissioning process, all visual observations and adjustments must be recorded for future reference. The system will begin to cool down as soon as CO2 in the liquid state is loaded into it. This causes the pipes to contract, with possible cracks between the joints of the same. The entire system must be inspected for any signs of leaks.
How do the equipment work with CO2?
Before starting the equipment it’s important to follow the following observations to avoid later expenses:m
- The operation of the control systems must be validated before loading CO2.
- Test engines at high and low level to verify capacities.
- The solenoid valves must be placed in automatic operation.
- The service valves must be configured in their position for system operation.
- The measuring or expansion valves must be adjusted to their calculated initial configuration.
- Confirm the operation of the defrosting mechanism, as well as the operation of the heater and its water flow.
- If the CO2 system is equipped with pumps, check the discharge pressure of each and pump in sequence to avoid the cavitation phenomenon.
Start-up tasks in CO2 equipment
Once the previous check, it is recommended to perform tasks associated with the boot:
- Activar compresores según recomendación del fabricante.
- Aplicar secuencialmente carga en los evaporadores.
- Tomar en cuenta las presiones del sistema y asegurarse de que sean según el diseño
- Después que la operación del primer evaporador y compresor se haya estabilizado, se agrega secuencialmente carga a evaporadores y compresores permitiendo un periodo de estabilización entre cada paso.
- Activate compressors according to the manufacturer's recommendation.
- Apply sequentially load in the evaporators.
- Take into account system pressures and make sure they are according to the design
- After the operation of the first evaporator and compressor has stabilized, it’s sequentially added to the evaporators and compressors allowing a period of stabilization between each step.
Optimizing costs doesn’t have to mean the acquisition of low quality equipment. It’s rather to know how to strategically use the equipment and have the appropriate engineering, designed specifically for each case. Although the role of engineering is often not valued, the truth is that this will be the main responsible for the success of any refrigeration project.
Related
Discover more related articles
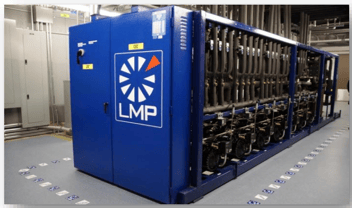
4 key points in the transcritical co2 system
The design of a transcritical CO2 system is a challenge even for a refrigeration expert. The correct implementation and quality of the equipment...
Read more »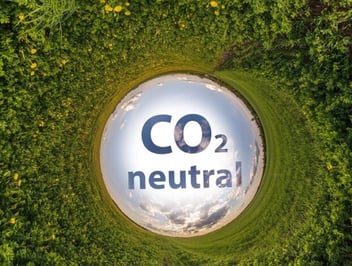