One of the most common challenges in the industrial refrigeration industry is to implement maintenance plans that ensure the useful life of the equipment and the energy efficiency that a project needs to function.
The lack of culture of prevention makes it difficult to convince the final customers of the need to invest in the different types of maintenance that the equipment require for maximum efficiency.
For a refrigeration contractor, maintenance is a difficult service to market, as many final customers think it is not necessary. However, there is a key element that makes the difference: trust.
If your industrial refrigeration services inspire confidence to your customers, this will generate better job opportunities, including maintenance service.
The difference between a large refrigeration business and a small one is the level of trust that it generates to final customers.
In this post we will recommend some useful measures that can help your refrigeration company to generate more value and realize business through the maintenance service.
1. Generate confidence to your final customers
In the business of industrial and commercial refrigeration, trust is essential to start a work relationship that is productive for the parties involved. For you as a contractor, it represents the opportunity to work on better projects, perhaps with a bigger budget, and for the client, the security offered by the quality of your work.
To generate this trust you must consider a careful system of good practices that include:
- Strict compliance between what your company offers and the result of the installation of a refrigeration project.
- Providing engineering and equipment suitable for the requirements of a project.
- Be clear about the delivery times and the costs of the equipment required.
- Carry out the post-sale service, offer guarantees and resolve conflicts that your final customer may face in the use of the equipment
- Deliver a report of the maintenance requirements for the specialized teams involved in the project.
Any company wishing to excel in the industrial refrigeration sector must comply with quality and efficiency at least 3 basic services:
-
Project development, calculation and engineering.
-
Adequate installation of refrigeration systems.
-
Maintenance programs for the projects that you develop.
In Froztec International we have 18 years working with various refrigeration contractors, which we support with specialized engineering and the selection of equipment with the best technology for the requirements of each project.
Recommended reading 👉🏽 Why choosing Froztec as your refrigeration support?
2. Recommend the use of a plan and maintenance policies
As stated earlier, a relationship of trust is the key. If your refrigeration company has found a good market niche in some area of industrial refrigeration, recommend to your customers the use of maintenance policies.
By knowing the equipment you are installing and confident of having the best specialized engineering that supports you, you can offer a policy that indicates the dates in which it would be necessary to perform a preventive maintenance work.
Preventive maintenance provides your customers confidence in the optimal functioning of their equipment and it also results in a considerable saving of resources compared to corrective maintenance.
Communicate to your customers that they can save more money by setting up maintenance plans with estimated dates, instead of waiting for a component to fail causing loss of merchandise or to stop the operation of equipment.
This not only favors your clients, it also allows you to ensure your work on a project. It is one more service that you can apply to improve your opportunities and provide for a full year's work.
For example, a refrigeration system that can be installed in the winter season may need a preventive check during the hot season.
Therewith we add value to your company, thanks to the fact that your service and the quality of your work guarantees its efficiency with the support of preventive maintenance that you can offer to your client.
3. Offer recommendations for use and types of maintenance of the refrigeration equipment
A cultural problem that occurs in several parts of the world is that those in charge of the supervision of a refrigeration system do not know the necessary guidelines for the maintenance of each component of the equipment.
Nowadays, several manufacturers of refrigeration technology offer meticulous operation and compatibility manuals, but there is little culture for consultation and full knowledge on the part of the final user.
Use this element in your favor, creating maintenance manuals or communicating the best practices for the care of the equipment.
There are many bad practices in the daily use of a refrigeration system. Identify them according to your industry and make recommendations to avoid them.
For example:
- In some industries, many cold room workers find it easy to dry their work coats with the heat expelled from the evaporator. This prevents the passage of air and lowers the efficiency of the equipment to the extent of damaging it.
- Some areas for processing products have serious damage to their equipment when they are washed while they are in operation. This also represents a serious fault that affects the useful life of the systems.
- Teach that cold room doors have an important function in the efficiency and care of the products. To calculate and realize that they should not remain open for a long time is important to guarantee the energy saving and the functioning of the equipment.
Do not forget to read 👉🏽 5 golden rules for the design of your cold rooms.
In Froztec International we have partnerships with contractors around the world who offer constant training programs for the use of specialized technology, this is a measure that we generate to positively impact the industry.
If you think that your company needs more knowledge of new technologies and industry innovations, consider that training is an investment in the future that will guarantee competitiveness in your market niche.
Offering maintenance manuals or a series of good practices allows you to put yourself in the role of expert before your clients and strengthen the confidence that you have in your business.
4. Document your maintenance or repair work on refrigeration equipment
A good practice for your refrigeration company is to document the work process.
Before starting to work in maintenance, take pictures prior, during and after a service
Document the steps you followed while working on the system and list the changes.
Nowadays it is not necessary to print documents, with your own cell phone or mobile device you can document all the processes:
- If there were changes of coils
- If the filters were renewed
- Deep cleaning processes
- Etc.
This habit is unusual in the industry and can generate good perception of your services, which can result in new work proposals.
5. Optimize your installation times of industrial refrigeration equipment
As you know, the first steps before working on the installation of a refrigeration project are the specialized engineering calculations and the selection of the equipment.
When you select the equipment, you depend on the times they take to be sent to the place of your project.
Knowing exactly the arrival times and making a schedule of your work allows you to save time and resources. Create your agenda according to the availability you have of the equipment.
In Froztec International we have alliances with the main manufacturers of industrial refrigeration technology. One of our services is to get this equipment in the right time.
In our experience, saving on transfers and taking advantage of all the time you spend on the construction site allows you to save money and time, which is, above all, the most valuable resource for every contractor.
6. Quote in dollars when necessary
Another erroneous practice in the industry is to quote equipment without taking into account the variation of the currency exchange rate.
Many of the specialized equipment are quoted in dollars, so when converting to the national currency, the price can vary from day to day and cause an unexpected fluctuation in your profits.
Consider quoting in dollars, this will allow you to avoid misunderstandings and have a good balance between your earnings and the investment required.
7. Grow your industrial refrigeration company with specialized support
Being competitive in the refrigeration sector is a constant challenge for contractors around the world. Deciding on new, more ambitious and larger projects requires technological support and constant updating.
In Froztec International we have experience in supporting international industrial refrigeration projects with specialized engineering and selection of first-class technological equipment that sustain the efficiency of each project no matter how complex it may be.
👉🏽Check our success cases in industrial refrigeration👈🏽
If your refrigeration company intends to grow or consolidate its influence, evaluate the advantages of having the support of engineering and cutting-edge technological equipment appropriate to the new challenges of the industry.
Related
Discover more related articles
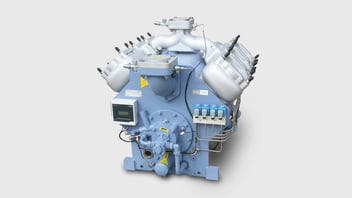
Guide: Main components and accessories of industrial refrigeration
The industrial refrigeration market is under constant growth and innovation; therefore, in order to be competitive, it is necessary to be up to date...
Read more »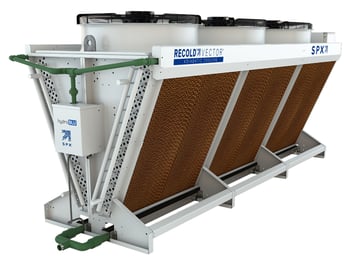